English
Schnellecke Logistics
Company Overview
Schnellecke Logistics is a leading global logistics company. Services include complete concepts from transportation, warehouse management and value-added services to module assembly and container-compatible packaging. With a global network and state-of-the-art technology customers’ supply chains are optimised. Schnellecke has a focus on innovation and sustainability in order to offer customized and future-proof solutions.
Location: Soltau, Germany
Industries: Automotive, Industrial and Consumer goods
Global Markets Served: Europe, Asia, Africa and North America
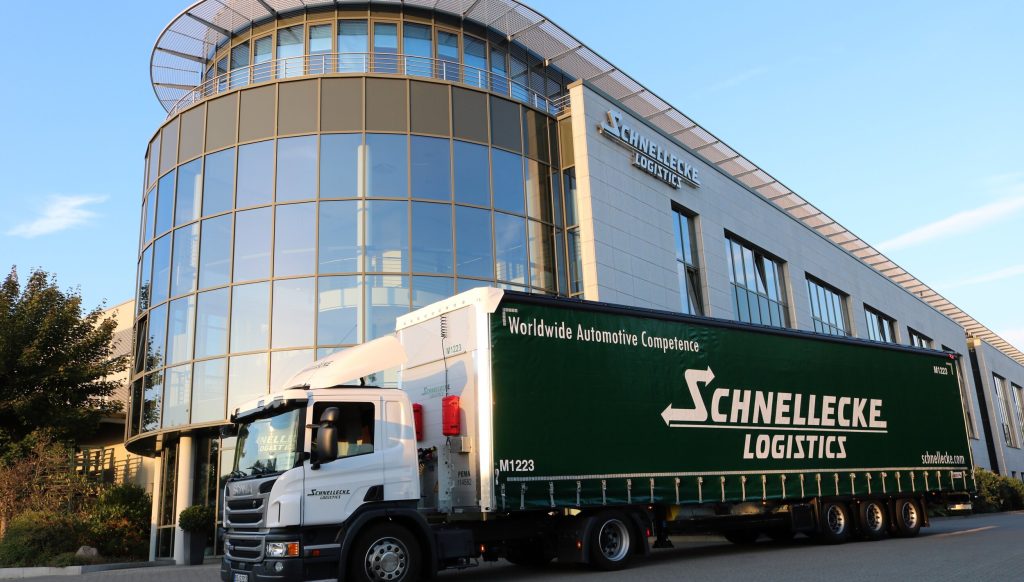
The Situation
Labour Management
Efficiency Optimisation
Flexibility Requirements
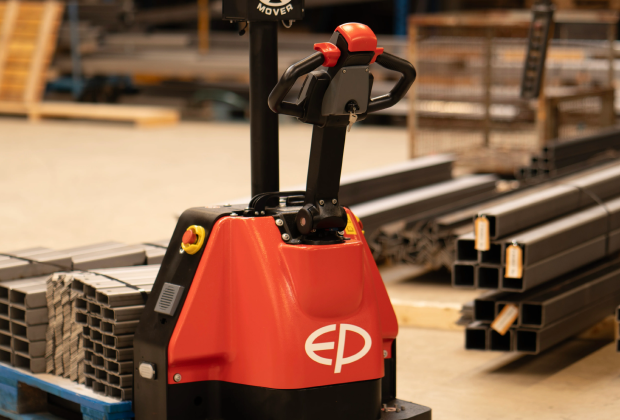
Scaling Across Europe
“EP’s product is the most flexible product compared to other products in the market for our use case.”
“All of our sites want XP’s – they are crazy. You guys are always on our mind.”
“Compared to more expensive automation solutions that require changes to existing processes, the XP15 integrates seamlessly into our current workflows. It is scalable and, with its various options and functionalities, fits a wide range of processes. The XP15 can grow alongside our company and adapt to evolving customer demands.”
Timeline
From First Call to Full Operation
Step 1: Call Scheduled
Schnellecke scheduled a call with EP Automation Experts.
Step 2: 15-minute Teams Meeting
The first 15-minute Teams meeting to discuss these points:
- Virtual site survey
- Job(s) to do
- Types of loads
- Material flow information
- Working conditions
Next step: A Walkthrough Video taken by the Schnellecke team and shared with the EP team.
Step 3: Define Project Scope
A 30-minute Teams meeting with the EP Automation experts. Based on the site survey and walkthrough video, together define the scope and a proof of concept.
Step 4: Delivery & Implementation
Delivery in Soltau
The XP15 is delivered from European stock.One Day On-Site Implementation with EP Team
✅On-site walkthrough with Schnellecke’s team
✅Teach the XP15 required tasks (Transport, column drop-off)
✅POC confirmed, the robot is operational by end of the day
✅Team training provided
✅Final handover: Schnellecke’s staff is ready to take over robot independentlyTraining and handover✅ User training
✅ Schnellecke’s staff is ready to take over robot independentlyNext Step
✅ Call Box as an add on option, to call the truck to the reception area when a pallet is ready for pick up. Installed by Schnellecke key user.
The Solution
“The XP15 fits our use cases without having to change our working environment to be able to implement the robot.”
Schnellecke partners with EP Equipment to implement the XP15, a co-bot solution tailored to the specific in-house pallet transportation needs. By automating repetitive A-to-B pallet transport, the XP15 significantly reduces traffic movements, and manual labour and enhances overall efficiency in intralogistics.
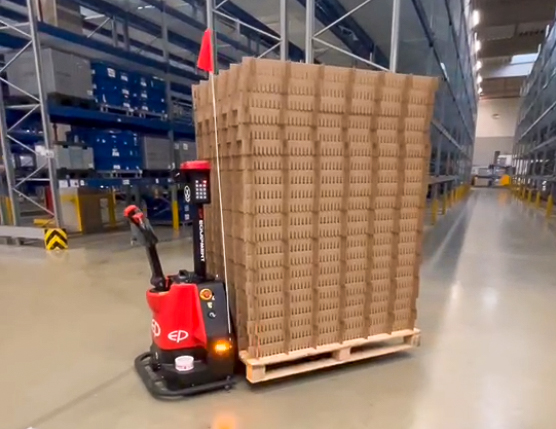
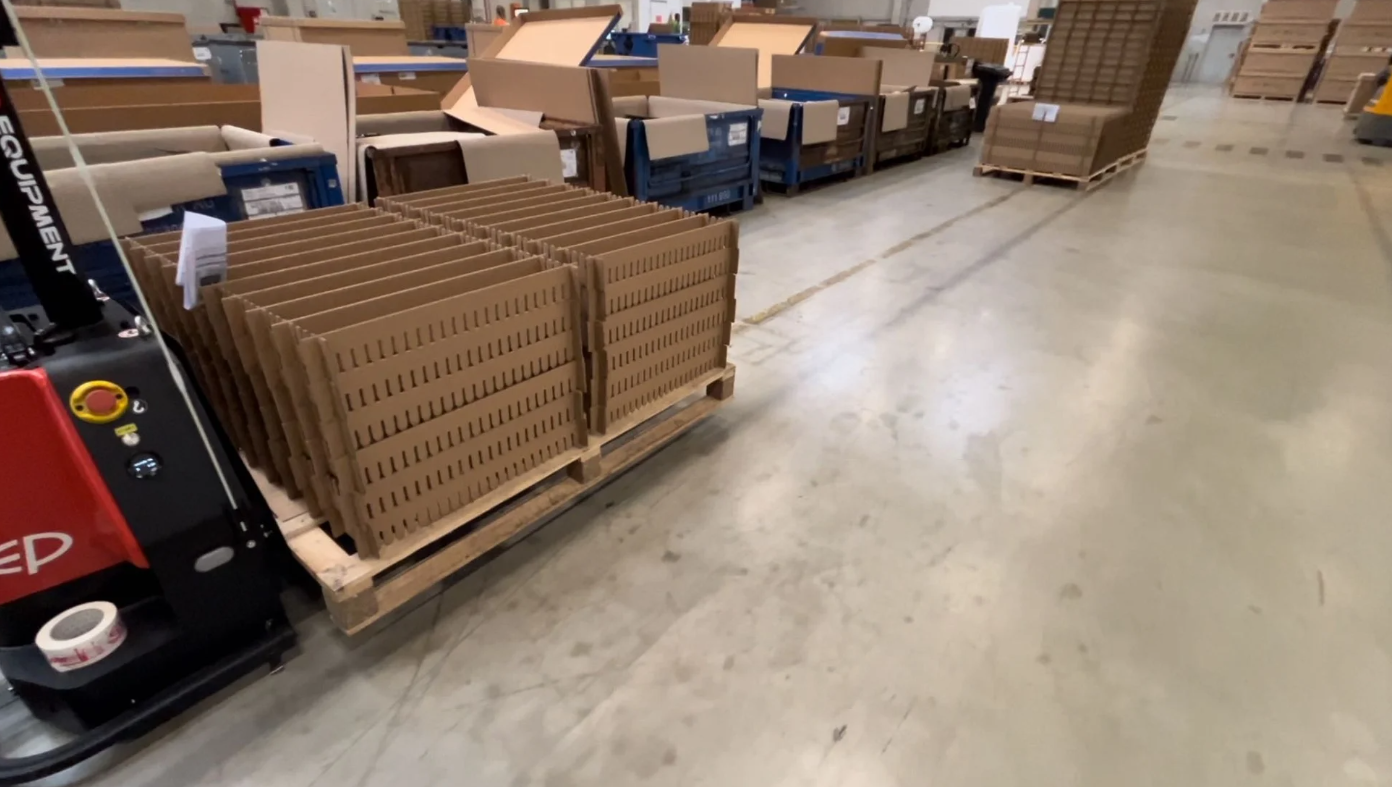
In-House Pallet Transport
Schnellecke utilises the XP15 to automate in-house pallet transport between the box production and packaging areas. A machine folds the boxes, employees manually load pallets with empty corrugated boxes at the production station and then assign tasks by pressing the respective numbers on the keypad.
The XP15 autonomously transports the pallets to designated destinations and returns to the production station. This solution not only addresses the shortage of human labour, but also allows employees to focus on more critical tasks at their workstations while the XP15 handles repetitive pallet transportation efficiently.
Call Box Solution
The Call Box is an add-on feature that enables warehouse employees to call the pallet truck to a designated workstation within the warehouse. With the press of a button, the truck will drive empty to the specified location, ready to start its next mission.
In this process, a pallet truck is called from the production area using the call box. It then collects a pallet loaded with empty KLT boxes from the reception area. Once the operator presses the button, the robot delivers the pallet to the designated hand shelf area. After completing the task, the robot returns to its parking location in the production area. This system ensures a seamless and efficient workflow.
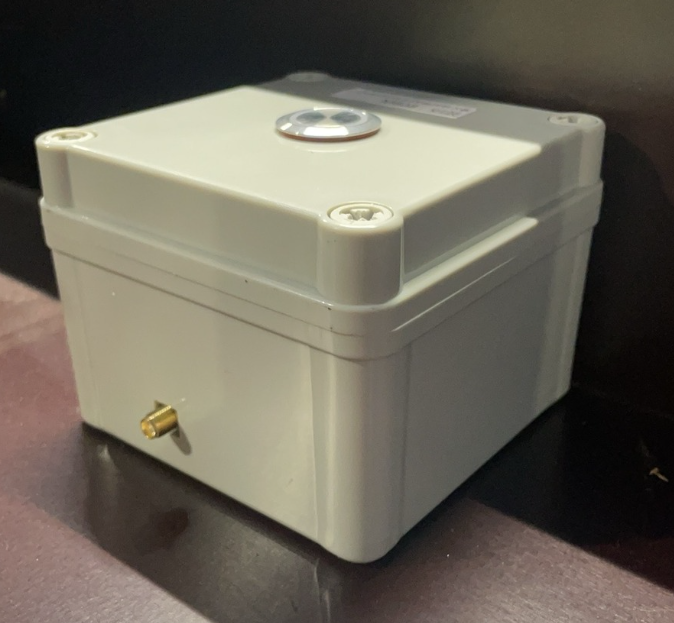
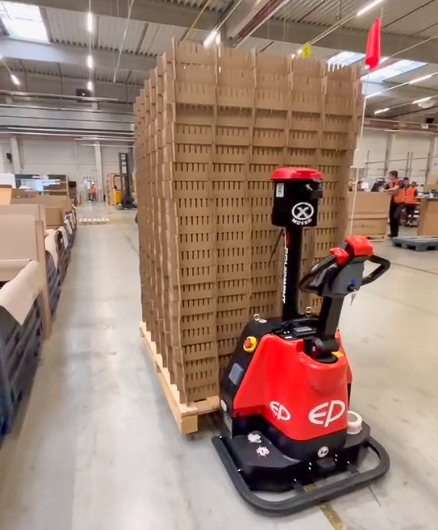
Automated Unloading Solution
“Other sites are recognizing the advantages of EP’s approach to automation. We’ve gathered various use cases showcasing its impact, with the XP15 proving to be a perfectly flexible tool for our employees”.
The XP15 drops off the pallets automatically at the work stations. The pallet truck drops the pallets in columns at designated drop-off points. The employees at the packing stations then have direct access to the stock of empty boxes. This allows employees to remain focused on folding and packing, improving productivity.
Uptime
Operating 2 shifts per day with an average runtime of 15–16 hours.
By automating the transport tasks, employees can focus on higher-value activities in the warehouse like packing and folding, while workforce productivity improves through the elimination of dead walking time.
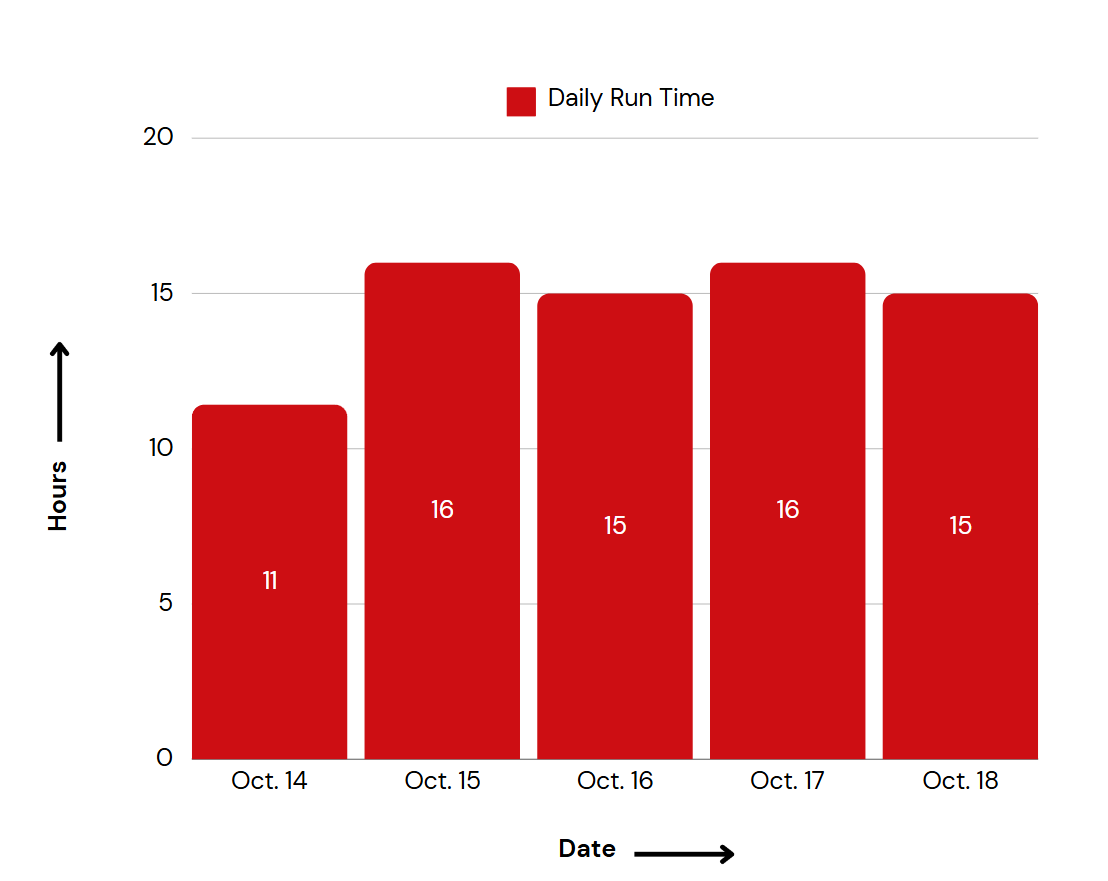
The Result
By implementing EP’s XP15, Schnellecke has successfully addressed their manual labour shortages and bottlenecks, as well as reduced operational costs while improving efficiency. The quick implementation, cost-effective automation, and flexibility of the XP15 Co-Bot have enabled Schnellecke to streamline repetitive pallet transport tasks, allowing employees to focus on higher-value activities in their logistics centre.
This scalable solution positions Schnellecke for continued growth and operational excellence across multiple European sites. The internal logistics engineering team brings the foundational expertise needed to drive the next steps forward in-house.
Why EP?
Scaling across Europe
The XP15 is ready to scale up automation across 20+ Schnellecke sites in Europe. Together with EP’s automation team, the Schnellecke logistics engineering team can successfully transfer solutions from one site to another, adapting to the businesses operational demands.
Quick Implementation
EP’s provides Schnellecke a flexible approach to scale without the need to change the working environment.
- 1-day machine setup
- No extensive calibration or prolonged testing periods
- From idea to installation in just 4 weeks
Affordable Automation
EP’s competitive pricing brings automation performance with instant ROI and low-risk, making automation accessible for its business units of all sizes. Furthermore it allows to automate as well the non-obvious processes such as empty pallets and waste containers.- €25,000 starting price or €995/month rental
- Alternative solutions cost start at €150,000–€250,000 and require up to a year for implementation
Easy, Flexible, and Adaptable
- Easily adjust paths, drop-off points, tasks
- Handle different load types & sizes
- Add new tasks according to your operation